The Role of Wire EDM in Producing High-Precision Components
Precision is the foundation of modern manufacturing, especially in industries like aerospace, medical, and commercial sectors that demand complex geometries, tight tolerances, and repeatability. One machining technology that meets these challenges is Wire Electrical Discharge Machining (Wire EDM). This non-contact process allows manufacturers to cut intricate shapes in hard materials with exceptional accuracy, making it indispensable for high-precision components.
What Is Wire EDM?
Wire EDM is a non-contact machining process that uses a thin, electrically charged wire to cut through metal. It works by creating a series of electrical discharges (sparks) between the wire and the workpiece, which erodes the material with extreme accuracy. Since the process does not involve any direct contact, it eliminates the risk of mechanical stress, making it ideal for delicate, high-precision components.
Key Features of Wire EDM:
- High precision – Achieves tolerances as tight as ±0.0001 inches.
- No mechanical stress – No physical tool pressure, preventing part deformation.
- Ability to cut hard materials – Works on materials like titanium, Inconel, and hardened steels.
- Complex geometries – Can create intricate shapes and fine details that traditional machining cannot.
How Wire EDM Works
Wire EDM operates using a thin brass or copper wire (usually 0.004” to 0.012” in diameter) as an electrode. The workpiece is submerged in a dielectric fluid, typically deionized water, which helps cool the part and remove debris. The electrical discharge between the wire and the workpiece erodes the material in a controlled manner.
Wire EDM Process Steps:
- Programming – The cutting path is programmed using CAD/CAM software.
- Submersion in Dielectric Fluid – The workpiece is placed in deionized water to control heat and flush away debris.
- Electrical Discharge Cutting – The wire moves through the workpiece, creating sparks that precisely erode material.
- Flushing & Finishing – The process continues until the desired shape is achieved, with minimal need for secondary finishing.
Why Wire EDM is Essential for High-Precision Manufacturing
1. Achieving Ultra-Tight Tolerances
For industries like aerospace and medical, even the smallest dimensional deviation can lead to product failure. Wire EDM enables exceptionally tight tolerances, ensuring parts fit and function as intended.
2. Cutting Hard and Exotic Materials
Many critical components require materials like hardened steel, titanium, and carbide, which are difficult to machine using traditional methods. Wire EDM can effortlessly cut through these materials without excessive wear on tools.
3. Creating Intricate and Complex Geometries
Wire EDM can produce sharp internal corners, thin walls, and tiny intricate details that would be impossible with conventional machining. This makes it ideal for medical implants, aerospace turbine blades, and precision tooling.
4. No Distortion or Tool Wear
Since Wire EDM is a non-contact process, it eliminates mechanical stress, preventing warping or deformation—critical for thin, delicate, or high-accuracy parts.
5. Cost-Effective for Prototyping and Small Runs
Wire EDM reduces material waste and requires minimal tooling, making it an efficient choice for low-volume, high-precision production and rapid prototyping.
Industries That Rely on Wire EDM
Many industries depend on Wire EDM for manufacturing small, intricate, and high-precision components. Some of the key sectors include:
- Aerospace – Engine components, turbine blades, and structural components.
- Medical – Surgical instruments, orthopedic implants, and micro-machined parts.
- Defense – High-performance weapon systems and electronic enclosures.
- Automotive – High-performance engine components and custom tooling.
- Electronics – Micro-components for circuit boards and semiconductors.
Modelcraft Co.: Precision in Every Detail
Wire EDM is a vital tool in modern manufacturing, providing unparalleled accuracy and versatility across industries that demand high-precision components. At Modelcraft Co., our AS9100D and ISO 9001:2015-certified facility combines decades of expertise with cutting-edge Wire EDM technology to deliver precise, reliable, and high-quality machined parts. Contact us today to discuss how we can support your next precision manufacturing project.
Recent Articles
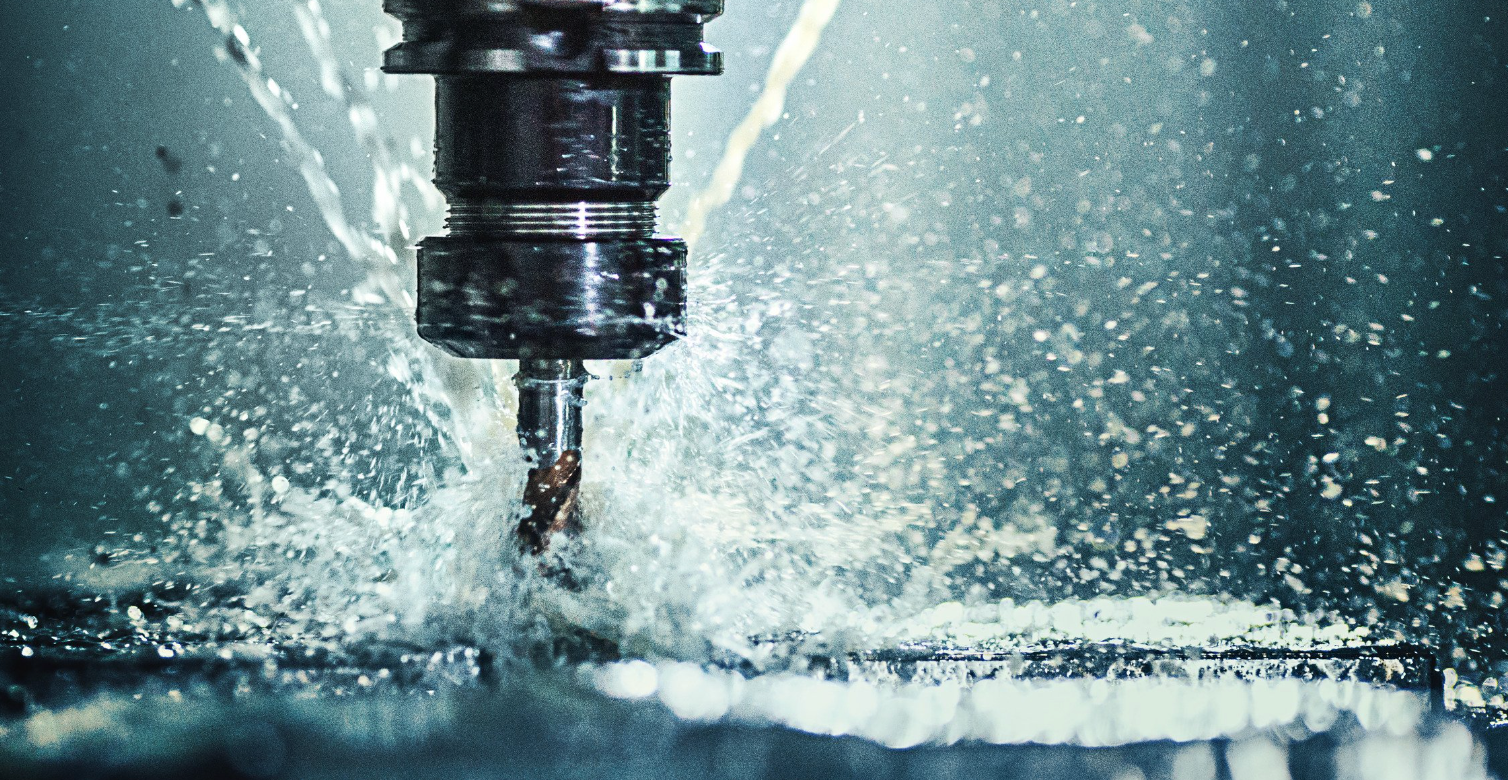